1. Introduction
Materials with capacitive properties are increasingly widely used in electronic devices and can be found in high-frequency electronic components, sensors, and various energy storage devices. The charge-discharge characteristics of these materials directly affect device performance in areas such as high-speed data transmission, sensor accuracy, and battery lifespan. Accurately measuring the charge-discharge behavior of materials under different working environments also helps researchers gain in-depth understanding of their electrochemical performance, including key parameters such as specific capacitance, energy density, power density, and cycle life. This data is not only crucial for the optimized design of materials but also provides a theoretical basis for material selection and performance evaluation in engineering applications. For example, the charge-discharge characteristics of supercapacitors and batteries directly determine their service life and power response, and precise testing can optimize their energy storage and release capabilities, thereby enhancing the overall efficiency of devices. To improve the design and application performance of these materials, accurately understanding their charge-discharge characteristics under different voltages, frequencies, and signal conditions is particularly critical.
However, traditional capacitance testing methods typically use fixed frequencies or fixed voltages for experiments, which cannot fully reflect the actual performance of materials in complex working environments. In many application scenarios, materials with capacitive properties are not in ideal working states but face variations in frequency and voltage. Especially under high-frequency, high-voltage, and variable signal conditions, the limitations of traditional testing methods are particularly prominent. The capacitance response, energy storage characteristics, and charge-discharge efficiency of materials under these extreme conditions may differ significantly from test results under fixed voltage or frequency. Therefore, developing a testing solution that can comprehensively evaluate the charge-discharge characteristics of these materials under dynamic working conditions is particularly important.
2. Capacitive Materials Overview
2.1 Liquid Materials
Liquid materials, especially some liquids with capacitive properties, have been widely used in electronic devices in recent years. For example, certain liquids (such as organic liquids, ionic liquids, etc.) inherently possess capacitive properties and can serve as working media for capacitors. The capacitive characteristics of these liquid materials mainly originate from their molecular structure and the movement of charges within the liquid. When an electric field is applied to the liquid, charged molecules or ions arrange themselves according to changes in the electric field, thereby forming a capacitive effect.
Liquid capacitors can achieve large capacitance values in relatively small volumes due to their high specific surface area and good electric field responsiveness. However, the capacitive performance of liquid materials is influenced by their conductivity, dielectric constant, and temperature stability. Therefore, when designing liquid capacitors, these characteristics of liquid materials need to be comprehensively evaluated, and the charge-discharge characteristics of liquid materials under different voltage and frequency conditions must be studied.
2.2 Wires
Wires, as a material with capacitive properties, are widely used in electronic devices. Their capacitive characteristics are mainly reflected in the charge accumulation and distribution behavior of wires under the action of an electric field. The capacitive characteristics of wires are closely related to factors such as their shape, size, material, and the dielectric properties of the surrounding environment. For example, as the length and surface area of a wire increase, its capacitance value also increases accordingly.
In high-frequency applications, wires exhibit significant capacitive effects, which directly affect signal transmission efficiency and stability. In practical applications, the capacitive characteristics of wires often play important roles in high-speed signal transmission, energy storage, and power transmission. To optimize the performance of wires under high-frequency and varying voltage conditions, research on the charge-discharge characteristics of wires is necessary.
2.3 Solid Metals
Solid metals, as conductive materials, are widely used in various electronic devices. They possess excellent conductivity, providing reliable electrical connections in high-performance devices. Particularly, nanoscale or surface-treated metal materials exhibit significant capacitive properties. Charge distribution and accumulation on metal surfaces form a capacitive effect, especially in high-frequency applications where solid metals exhibit low resistance, significantly enhancing their capacitive characteristics.
As metal dimensions decrease, surface capacitive effects are strengthened, thereby improving their capacitive performance in high-frequency signal transmission and storage. The capacitive characteristics of solid metals have broad application prospects in fields such as capacitors, sensors, and integrated circuits. Especially under high-voltage and high-frequency working environments, solid metals can provide higher energy density and more efficient charge-discharge performance.
3. Specific Test Solution
To address the above materials with capacitive properties, our company has introduced a test solution based on a DAQ system and an arbitrary waveform generator, which can effectively test the charge-discharge performance of different types of materials.
3.1 Test System Setup
First, connect the arbitrary waveform generator to the material under test (MUT) in parallel. The arbitrary waveform generator outputs varying excitation signals through a BNC interface, and alligator clips can be used during connection to ensure a secure connection. The signal source provides multiple waveforms to simulate the charge-discharge process of the material under different working environments.
Next, connect the data acquisition (DAQ) system. To measure voltage and current, connect the voltage measurement port of the DAQ system in parallel with the MUT. The voltage port uses a male banana plug connector to accurately record voltage changes across the material. The current measurement port is connected in series with the MUT, and the current port uses a female banana jack connector to ensure precise capture of current signals during the charge-discharge process.
Through this connection method, the test system can simultaneously acquire voltage and current signals, thereby comprehensively evaluating the dynamic charge-discharge performance of the material. Ensuring stable signal transmission and accurate data acquisition are key elements in the test system design. The block diagram of the test system principle is as follows:
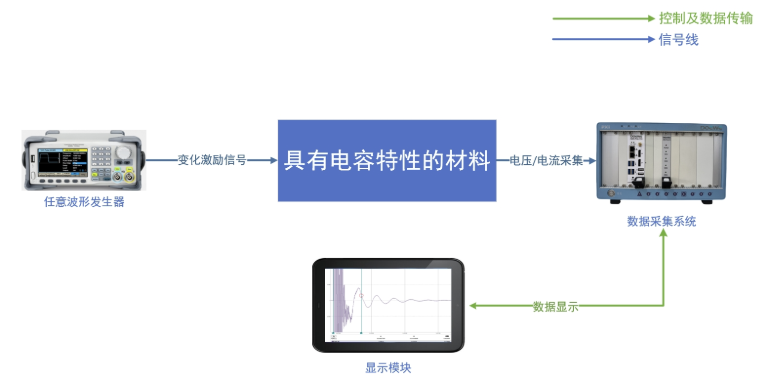
Figure 1 Test Principle Block Diagram
3.2 Test Method
3.2.1 Waveform Generation and Loading
Before starting the test, use the graphical editing software accompanying the arbitrary waveform generator on the computer to design the shape and amplitude of the output waveform according to experimental requirements. For example, a staircase waveform can be selected with an amplitude set to ±1V. After designing, save the waveform file and transfer it to the arbitrary waveform generator via a USB drive to complete waveform loading.
3.2.2 Signal Output and Data Acquisition
After connecting and configuring all test equipment, turn on the arbitrary waveform generator. Select the appropriate output signal frequency and waveform type, then start the signal output. Use the DAQ system to acquire the voltage and current changes of the MUT in real-time, monitoring its charge-discharge characteristics.
3.2.3 Frequency Variation Test
To study the charge-discharge characteristics of the MUT at different frequencies, gradually increase the frequency of the output signal and record the corresponding voltage and current changes. Special attention should be paid to ensuring that the output signal frequency remains below half of the DAQ device's sampling rate to avoid data acquisition distortion or inaccuracy.
3.2.4 Voltage Variation Test
If it is necessary to observe the charge-discharge characteristics of the material under different voltages, multiple waveform signals with the same frequency but different amplitude values can be edited and outputted one by one for testing. Record the test results promptly after each test. This data will be used for further analysis of the capacitive characteristics of the material under different working conditions.
3.2.5 Data Organization and Saving
After completing all tests, organize and save the data for subsequent analysis and discussion. Ensure all data files are complete and formatted correctly to facilitate later data processing and result verification.
3.3 Test Solution Analysis
By analyzing the voltage and current change curves of the MUT under excitation signals of different frequencies, voltages, and waveforms acquired by the DAQ system, the dynamic charge-discharge performance of the material can be comprehensively evaluated. The influence of frequency on charge-discharge characteristics is crucial. At different frequencies, the capacitance response and energy release characteristics of the material will vary. Especially under high-frequency conditions, the charge-discharge efficiency, energy density, and power density of the material will be significantly affected. Voltage also has a direct impact on the dynamic charge-discharge characteristics of the material. By changing the voltage of the excitation signal, the stability and charge-discharge efficiency of the material under different voltages can be tested. Voltage changes typically affect the capacitive characteristics and internal resistance performance of the material, thereby influencing energy storage capacity and release efficiency.
Furthermore, different waveform shapes (such as staircase waves, sine waves, square waves, etc.) have varying effects on the charge-discharge characteristics of the material. The waveform shape determines the rate of change of the excitation signal, which in turn affects the response characteristics of the material. By comparing charge-discharge curves under different waveforms, an in-depth understanding of the material's performance under different working conditions it may face in practical applications can be gained. This is particularly important in signal transmission and sensor applications.
The core advantage of this test solution lies in the DAQ system. The DAQ system supports high-precision, high-ADC-accuracy long-duration signal acquisition, enabling stable and accurate recording of the charge-discharge behavior of materials under different working conditions. The DAQ system not only ensures the accuracy of data acquisition but also enables comprehensive monitoring of material performance under complex conditions such as long-term, high-frequency, and high-voltage operation. Through comprehensive analysis of this test data, the energy storage characteristics, current response, and voltage stability of the material can be accurately assessed, providing an important basis for the optimized design and practical application of the material.
4. Introduction to Core Test Equipment
4.1 Arbitrary Waveform Generator
The arbitrary waveform generator is a device widely used in testing and research, capable of generating various waveform signals, including basic waveforms such as sine waves, square waves, and triangular waves. Additionally, with the accompanying waveform editing software, users can custom-design the shape, amplitude, frequency, and other parameters of test signals on a computer. This functionality enables the arbitrary waveform generator to meet signal requirements under different experimental conditions, making it particularly suitable for dynamic charge-discharge characteristic testing.
This device supports a wide range of frequency and voltage amplitude adjustments, capable of simulating various actual working conditions—from low frequency to high frequency, low voltage to high voltage—allowing precise settings to meet the demand for signal diversity in material testing. Its high-precision control system ensures the stability of signal output, avoiding waveform distortion or instability during testing, thereby improving the accuracy and reliability of test data.
4.2 Data Acquisition (DAQ) System
The DAQ system is the core equipment of this test solution, responsible for real-time acquisition and recording of current and voltage signals generated during the testing process. This system is equipped with high-precision two-channel current signal acquisition and two-channel voltage signal acquisition functions. The sampling rate reaches 2 MS/s, and the bandwidth covers DC to 300 kHz, ensuring the ability to capture subtle current changes during the dynamic charge-discharge process of the material. The system uses 4mm isolated banana plug interfaces to ensure stable signal transmission and reduce noise interference.
The measurement range of one current channel is 0.4 A<sub>RMS</sub>, suitable for capturing low-current signals, while the measurement range of the other channel is 2 A<sub>RMS</sub>, capable of handling larger current signals. This dual-channel design enables the DAQ system to adapt to test requirements across different current ranges, providing broader application scenarios.
The sampling rate of the two voltage acquisition channels is also 2 MS/s. The input range for both is 5 V<sub>RMS</sub> (±10 V<sub>PEAK</sub>), with a bandwidth of DC to 300 kHz. The measurement range of the voltage acquisition system is 300 V CAT III / 600 V CAT II, supporting accurate measurement in high-voltage environments and ensuring reliable data even in high-voltage testing. These voltage channels use 4mm isolated male banana plug interfaces, providing stable connections and signal acquisition.
Furthermore, the accompanying DAQ software allows users to view test conditions in real-time during experiments and save/export test data through the software interface. This software not only supports data visualization but also allows exporting test results as needed, facilitating subsequent data processing and analysis.
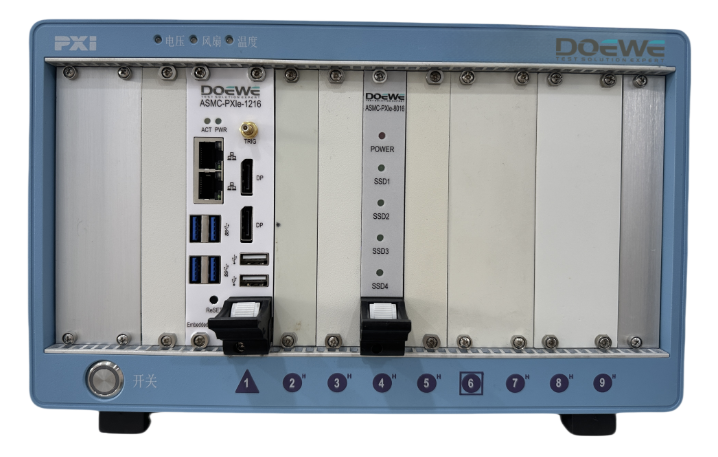
Figure 2 Data Acquisition System
5. Conclusion
The dynamic charge-discharge characteristic test solution for capacitive materials based on a DAQ system proposed by Doewe Technologies can accurately simulate the charge-discharge behavior of materials under changing amplitude and frequency conditions, thereby comprehensively evaluating their capacitive performance. Through the implementation of this solution, the charge-discharge characteristics of materials can be deeply understood in variable working environments, particularly under the influence of different signal amplitudes and frequencies. This provides reliable data support for material design optimization, performance enhancement, and application.
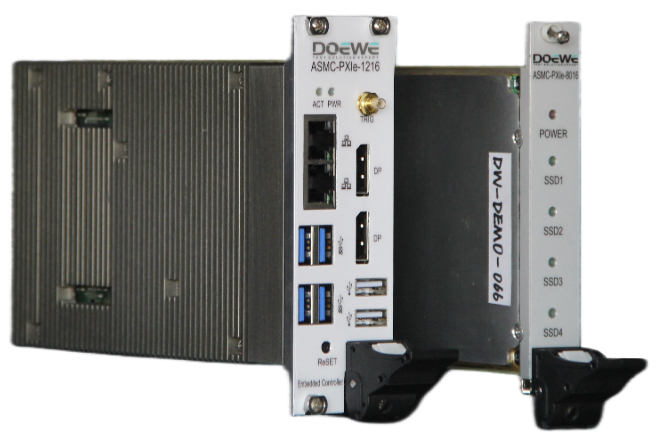
Figure 3 Data Acquisition Module
Doewe Technologies is always committed to achieving innovative, unique, and reliable product solutions in the field of data acquisition. We deeply understand that these elements are the cornerstone for enterprises to establish themselves in market competition. Precisely for this reason, our inspiration for innovation comes from the real application needs of customers, not merely to showcase flashy product features. By continuously optimizing and enhancing data acquisition solutions, Doewe Technologies empowers partners to move towards an efficient and precise future. Welcome to choose Doewe Technologies to jointly open a new chapter in data acquisition. Contact phone: 010-64327909.